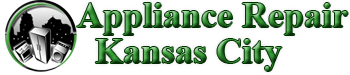
How To Fix A Dryer
Power Supply 240 Volts at Outlet
Test Fuses for Resistance and Condition
Check Motor For Proper Wiring Operation
Check Timer or Control Board For Directed Volts
How To Repair A Dryer That Doesn't Work ?
If clothes begin taking too long to dry, there usually is a build up of lint and debris in the exhaust vent. The first thing is to pull the dryer out so you have room to move and work. Then pull the vent duct off the dryer and check for debris and massive amounts of lint that may have accumulated inside the opening. In addition, check the outside vent to make sure it is not clogged. Most dryers lint screen only collect about 30-40% with the rest expelled through the outside vent.
Another thing to check if clothes are taking too long to dry is the placement of your dryer. Make sure your dryer has not been pushed back up against the wall. This can pinch the hose and cause a restriction in air flow from the back exhaust panel. To test, start the dryer and let run for a few minutes then open it up and feel if it is warm inside the drum. If there is no heat then you may have a thermal fuse or heat element issue. If there is heat inside the drum, your problem is not the dryer but the venting and you will need to find the choke point.
If your dryer starts up but doesn't heat you need to check the fuses and the element. The thermal fuse works as a heat-sensitive safety fuse which is attached to your dryer's exhaust duct. The design is for the fuse to blow when the dryer overheats. A fuse that has blown will cause your dryer to not heat. Moreover, in some cases, it may even keep the dryer from starting and turning on.
If your fuses test ok, then you may have an element issue. The dryer part that most people think goes out is the heating element. However, on occasion, the dryer element does go bad. If this is what has happened, then you will need to test the element to see if it has continuity. Continuity means it can carry an electrical current. In addition, an Ohms test gives you a resistance reading. These tests are usually all you need to do to know if you need a new element. If there is no continuity or resistance then you need a heating element.
Another area of frustration is when the dryer stops tumbling. When a dryer does not tumble it is usually a broken belt. Dryers use a belt that goes around the drum and connects to a motor drive shaft. The belt and motor is what turns the drum. If the belt breaks and fails it will stop turning the drum and clothes will not tumble. To check this you will have to open up your dryers' cabinet and inspect the belt. (see video step by step). Replace the belt if it is worn and broken. When you check the belt be sure and observe the idler pulley wheel. The pulley usually wears at the same rate as a dryer's belt and may need to be replaced too.
If a dryer starts to make a loud noise when tumbling you will need to check the drum rollers. These rollers are located in the back and are attached to the wall of the dryer. A common breakdown is the roller and bearing at the shaft. To fix a dryer that is making a loud noise you will need to open the cabinet. Start by removing the drum. At this point you will want to inspect the drum felt and the roller wheels. One of the areas that get a lot of friction wear is the felt and roller. You are looking to see if the wheels move freely or do they bind and wiggle when they turn? If the rollers are broken replace and be sure and check the shafts too.
The other area that can make a lot of noise is the felt. If the felt is worn out it will rub up against the metal and start degrading to a point it will need to be replaced. The felt rides on the back wall and seals the drum to the back. The noise you will hear is a loud swishing sound. The felt will need to be taken off and replaced the same way with new felt and glue.
Lastly, if the dyer makes a loud grinding noise when starting, it is more than likely the motor is going bad. This can be replaced but is an expensive repair. Depending on the age of the dryer and expense of your particular motor it may be better to retire the dryer. Most times it is too much of an expense. Our recommendation is to retire the dryer.
These issues are all fixable and do not necessarily require a new dryer. However, you have to determine if the age is too old or you are just ready for a new dryer. In any case knowing these symptoms can save you money and should help you get the most out of your repair.
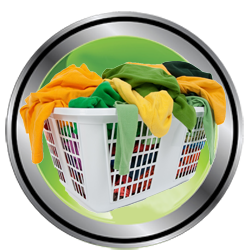
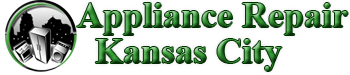
For all your Appliance Repair Service Needs KC Appliances is here to help get you back to normal. Located in 2411 MO 291 hwy, Independence, MO 64057. We can always be reached at 877.983.4933 or 816.286.4445